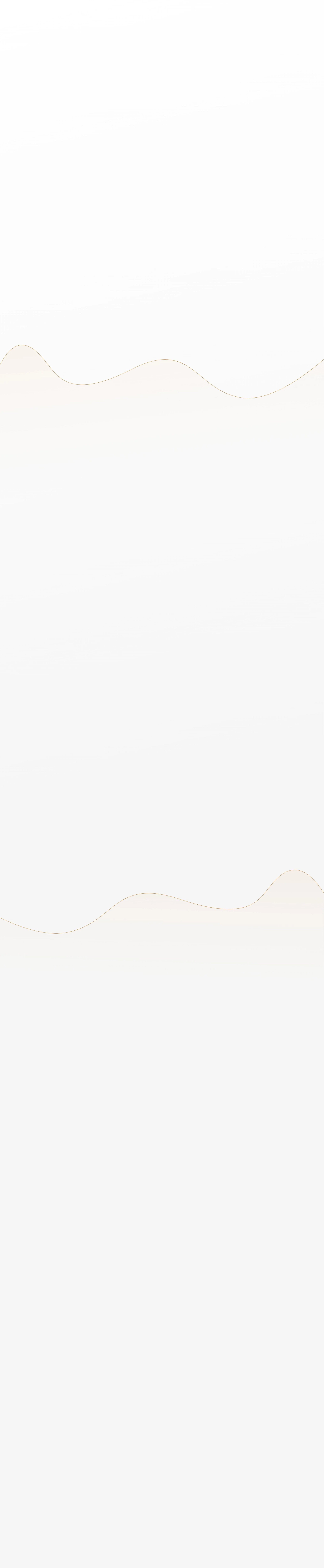
VP, UX Design Lead
Engagement Location: Columbus, OH
Engagement Goals
Integrate legacy systems and create efficiencies
GlobalFoundries was suffering from layers of legacy programs. They brought us in to identify how to create a more efficient workflow for a subset of their users.
Outcome
A truer understanding of business inefficiencies
While conducting user interviews and observing employees, we arrived at a key revelation - all the software interfaces were only associated with four fundamental entities: lots, holds, equipment, and inhibits. This crucial insight enabled us to propose a significantly more efficient and streamlined solution.
What is GlobalFoundries?
Semiconductor Manufacturer
GlobalFoundries (GF) is a semiconductor manufacturer with many recent acquisitions. Their expansion has led to growing pains associated with incompatible legacy systems. This has caused large inefficiencies for the business and individual employee workflows.
What is the problem?
Help identify the problem
"How can we create more efficiency" was essentially the entire prompt. GF knew the software was sluggish and bloated causing painful daily operations for employees. But that's where the internal direction ended.
Personas
The format
The company was fortunate enough to have large growth over the last decade, but integration between their fabs worldwide was starting to cause concerns.
Workflow inefficiencies
Growth through acquisition
As GF added fabrication centers to its portfolio there were many obstacles in consolidating the way each fab operated.
Inconsistent software and machinery
Everyone knew it could be better, but no one knew what would make a difference.
Tom has been with GlobalFoundries since 2016. His main responsibility is ensuring that the tools in his module are functioning according to plan and on schedule. He spends most of his shift intaking and analyzing complex data to identify what tools need to be prioritized to maximize his module’s utilization of both equipment and employees.
Tom - Shift Manager
Sasha has been with GlobalFoundries since 2019. Her main responsibility is to balance the flow of the lots and ensure the line is running smoothly. She spends her work day jumping from application to application to monitor and control the status of the lots ensuring holds stay down and the line is running efficiently.
Sasha - Operator
Research - Overview
We started interviewing operators and managers. Truthfully, there were so many variables that we felt we couldn't
draw any conclusions.
We shifted our focus to scheduling shadowing sessions for each of our in-scope programs. Things started to come together after after a long bout of doubt. But the process always produces results.
Research - Personas
Compounding variables uncovered
As our individual interviews started, we felt inundated with information. We reached out to folks who were recommended as operators that called themselves process techs or wafer fab techs. Our recommended shift managers were calling themselves production managers and manufacturing engineers. And amongst that confusion all roles suggested they touched all of the responsibilities across both roles.
Role titles
Shift Manager
Operator
Wafer Fab Technician (WFT)
Process Engineer
Role responsibilities
Tools
Production
Lots
Work in Progress (WIP)
Fabs (*Multiplier)
8 fabrication centers worldwide.
Equipment (*Multiplier)
Depending on the fab the equipment might be different models, versions, or in different locations
Software (*Multiplier)
Depending on role, fab, or preference software used might differ.
Common Goals Across Roles
Maximize tool efficiency
“I hold my team accountable for tool utilization and efficiency. If the tool isn't loaded it's going to subtract from that toolset for the day. If people are maximizing the WIP that can run on the tools our utilization will be high. High numbers is a direct reflection on our success to run the module.”
-Michael, Production Shift Manager, Fab 8
Maximize wafer output
“My main goal is to get wafers moved from the beginning of line to end of line and out as quickly as possible. They also have to be good wafers, so it’s not just about getting them out.”
-Deborah, Process Technician, Fab 9
Research - The Programs
Consolidated sample
A confusing constant
Through our shadowing sessions the only consistencies we recognized immediately were the innconsistant workflows used to get the same desired information across our personas.
Research - Findings
Distilled themes
A breakthrough in understanding
Research Distillation - Personas
Research Distillation - Future State Journey Map
Improvement metrics from simulations
Redirecting waiting LOTs (Holds)
Adjusting Equipment Load (Inhibits)
Finding High-Priority Tasks